Multiple Printing Pattern Custom
Our factory owns a variety of printing process tools and equipment, enabling customization with digital direct printing, digital sublimation printing, heat transfer printing, screen printing, puff printing, hot stamping printing, embossed printing, flock printing, and crackle printing, which could meet different customer needs by offering flexible small order customization and bulk order oem production.
Digital Direct Printing
We use Japanese Brother brand computer digital direct printing machine, which adopts environmentally friendly inkjet. The colors are vibrant, and the images are sharp, fully showcasing detailed designs with level 4 color fastness. Unlike thick coatings on fabric surfaces, this process preserves the softness and comfort of cotton materials.
We ensure vivid colors and clear patterns by precisely controlling ink mixing and print accuracy. By pre-treating the fabric, we enhance ink adhesion and prevent fading or peeling of the print. After printing, drying and curing processes are applied to ensure the durability of the printing.
Fabric Required: 100% cotton, which can absorb water-based ink well, resulting in vibrant colors, sharp details and high quality printing effects.
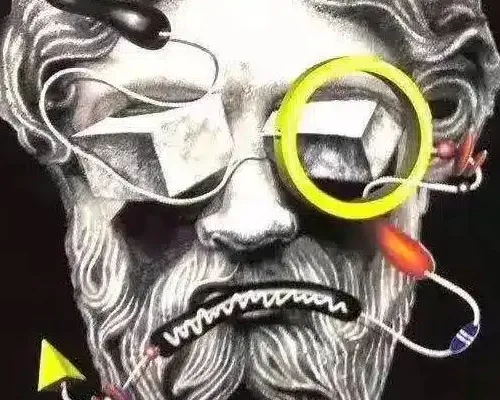
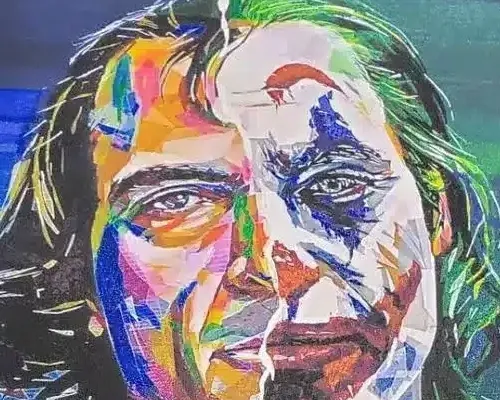
Digital Sublimation (All-over) Printing
We use Epson computer digital sublimation printing machine, the heat press transforms the sublimation ink into gas, which penetrates the fabric fibers to achieve the print. After heating, the fabric is cooled to ensure the ink firmly adheres.
During the printing process, we maintain color saturation and fine detail in the design. After printing, we check the printing results to ensure the colors are vibrant, the design is clear, and there are no deviations, ensuring the quality of the product.
Fabric Required: 100% polyester, which is ideal for digital sublimation printing due to its dense molecular structure, high heat resistance, smooth surface, and low moisture absorption, enabling vibrant colors and sharp patterns.
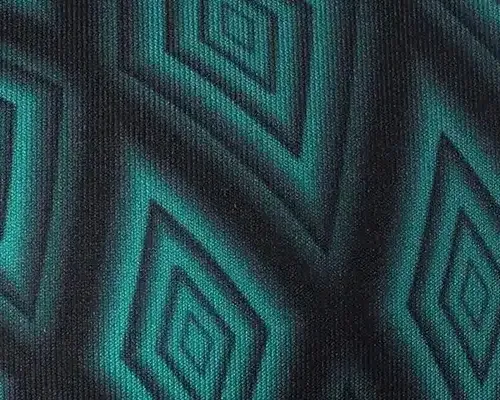

Heat Transfer Printing
We use Epson heat transfer printers and high concentration, sun-resistant heat transfer ink to achieve more vibrant colors, improved resistance to sunlight and washing, and longer lasting durability.
After the transfer is completed, a non-stick heat press sheet is placed over the design and pressed again for 5-10 seconds, which will reduce the risk of cracking or peeling.
Fabric Required: 100% polyester, which is ideal for heat transfer printing due to its dense fiber structure, high heat resistance, smooth surface, and low moisture absorption, ensuring sharp details and rich, durable colors.
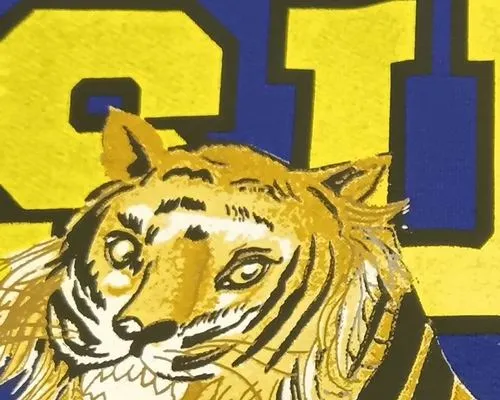
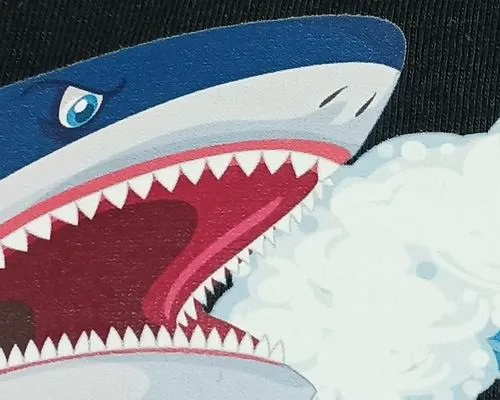
Screen Printing
For designs with relatively simple colors and lower precision requirements, we still use traditional screen printing, but choose inks with high pigment concentration and saturation.
Experienced technicians evenly scrape the ink across the screen by squeegee, after each shaving, they will check the ink uniformity and print quality to make sure there are no missed areas or uneven ink distribution.
Fabric Required: 100% cotton, which is perfect for screen printing, has strong ink absorption, making it suitable for various screen printing techniques.
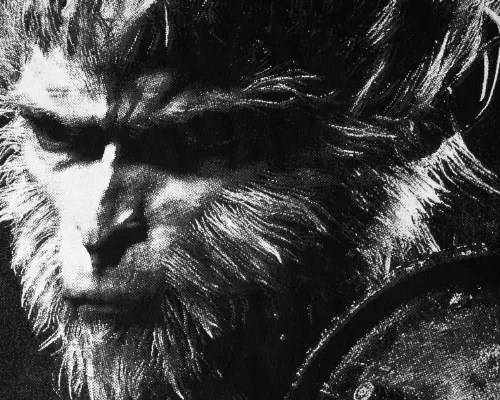
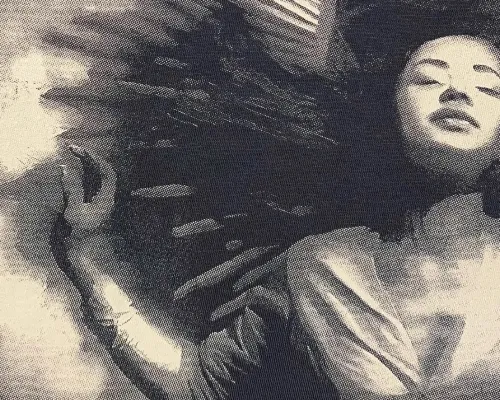
Puff Printing
For customers’ 3D printing needs, we add expanding agents to the ink, allowing the design to expand when heated, creating a 3D embossed effect. In printing, we precisely control the proportion of puff agent and ink to ensure even expansion and select the appropriate mesh screen to maintain ink flow and design clarity.
We also strictly regulate squeegee pressure and speed to ensure uniform ink transfer, preventing excessive thickness or blurring. By controlling heating temperature and time, we prevent over-expansion, scorching or insufficient expansion that could affect the final 3D effect.
Fabric Required: 100% cotton, whose absorbency allows better adhesion of puff print coating, ensuring a firm bond that prevents peeling.
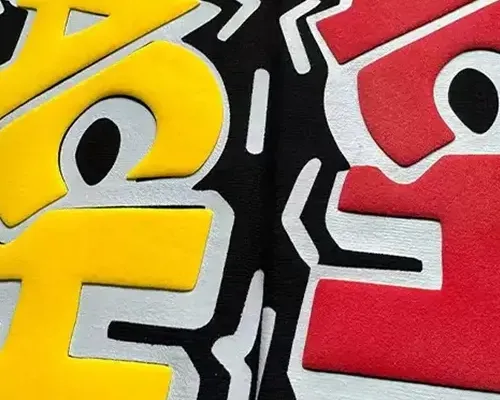
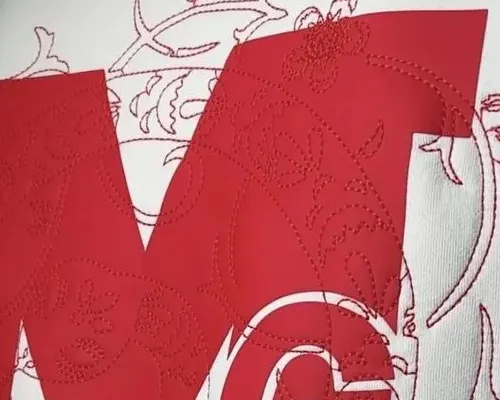
Hot Stamping
We started to make hot stamping processes such as gold/silver/reflective material hot stamping, which use heat and pressure to transfer metal foil or reflective materials to the surface of fabric to highlight metallic luster or reflective effect.
By controlling the temperature, pressure, metal foil selection and heating time, we ensure that the pattern is clearly and evenly transferred. After heating is completed, the cooling and peeling process is also strictly controlled to ensure that the foil is peeled off after cooling to the appropriate temperature to avoid damage to the pattern.
Fabric Required: 100% cotton, which is perfect for hot stamping prints due to the strong moisture absorption of cotton, which helps the prints film adhere effectively.

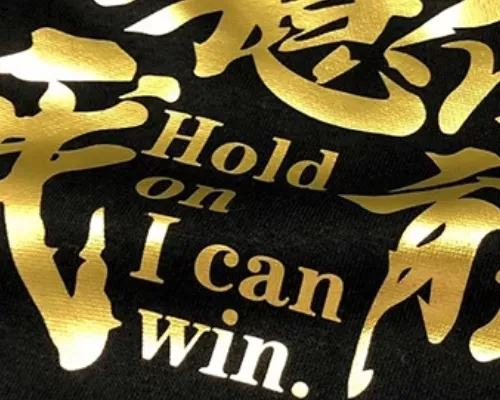
Embossed Printing
We also offer embossed printing, where high temperature and pressure are used to press the mold pattern onto the fabric, creating a 3D embossed effect.
We ensure precise design and mold production, select suitable fabrics, control heating temperature, pressure and time. After embossing, we allow for stable cooling and conduct quality checks to ensure the embossed effect is clear and uniform.
Fabric Required: 100% cotton, whose absorbency may make the embossed effect’s lines more delicate, resulting in clearer 3D details, and enhances the durability of the embossing.
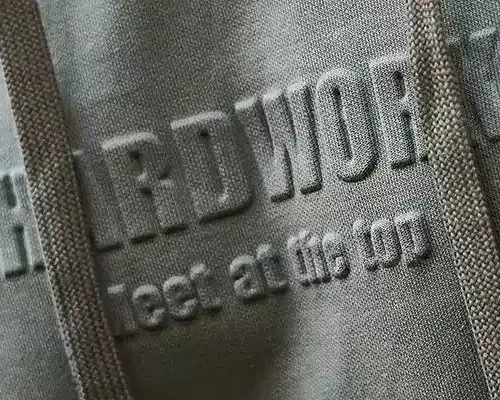
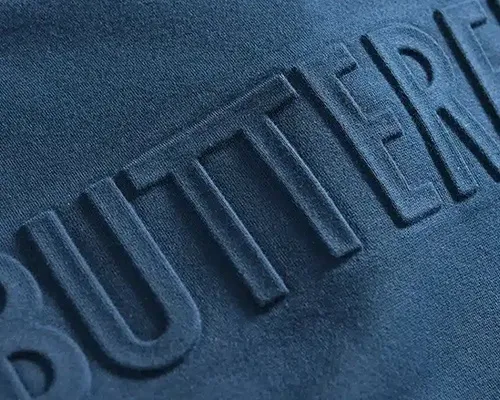
Flock Printing
We also offer flock printing, which involves applying adhesive glue on the fabric, followed by sprinkling fine fibers. After heating and curing, it creates a 3D and plush effect.
We evenly apply adhesive glue and sprinkle fibers, precisely controlling the heating and curing time and temperature to ensure a firm flocking effect and clear patterns. Excess unadhered fibers are removed, and the plush surface is trimmed to ensure the flocking effect is neat, stable and durable.
Fabric Required: 100% cotton, the loose fiber structure of cotton provides good adhesion, ensuring the flock particles remain firmly attached and maintaining the print’s longevity.
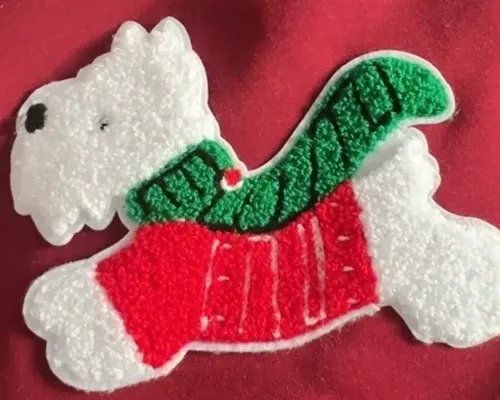
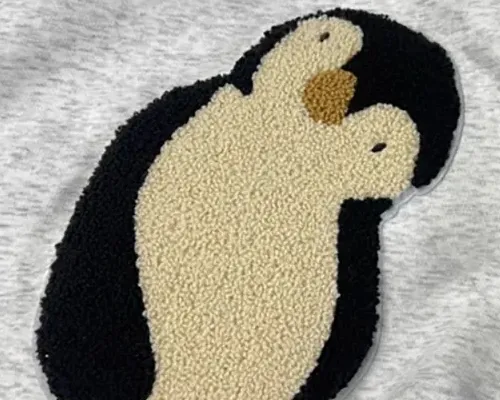
Crackle Printing
We also offer flock printing, which involves applying a base coat to ensure ink adhesion, and after the base coat dries, crackle ink is applied. This ink typically contains special ingredients that expand and form a crackled effect during the heating process.
We evenly apply the base coat to ensure good ink adhesion and uniformity. By precisely controlling the heating time and temperature, we ensure a well-defined crackle effect and clear patterns.
Fabric Required: 100% cotton, the excellent absorbency of cotton fibers ensures that the crackle print bonds tightly with the fabric.
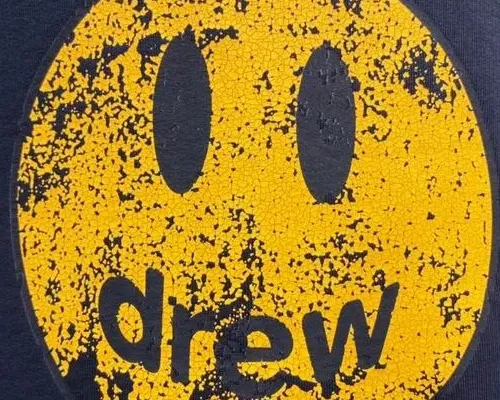
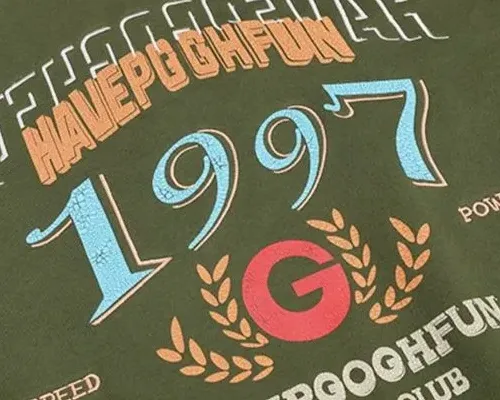